STEPPER MOTORS |
A stepper motor (or step motor) is a brushless DC electric motor that can divide a full rotation into a large number of steps. The shaft or spindle of a stepper motor rotates in discrete step increments when electrical command pulses are applied to it in the proper sequence, and the motor's position can be controlled precisely without any feedback mechanism (an open-loop controller), as long as the motor is carefully sized to the application.
Stepper motors may be used for locomotion, movement, positioning, and many other functions where we need precise control of the position of a shaft, lever or other moving part of a mechatronic device.
Stepper motors are formed by coils and magnets and incorporate a shaft that moves when power is applied. The difference between stepper and DC motors is the way the shaft moves. The rotor moves by applying power to different coils in a predetermined sequence. The stepper motor can also hold their position and resist rotation. |
How Stepper Motors Work? |
Stepper motors convert digital information into proportional mechanical movement. They are digital and different from DC motors that are controlled by changing the current across them. The electromagnets of a stepper motor are energized by an external control circuit, such as a microcontroller. To make the motor shaft turn, first, one electromagnet is given power, which makes the gear's teeth magnetically attracted to the electromagnet's teeth. When the gear's teeth are aligned to the first electromagnet, they are slightly offset from the next electromagnet. Thus, when the next electromagnet is turned on and the first is turned off, the gear rotates slightly to align with the next one, and from there the process is repeated. Each of those slight rotations is called a "step", with an integer number of steps making a full rotation. In that way, the motor can be turned by a precise angle. |
Types of Stepper Motors |
Stepper motors are available in three basic types; which are permanent magnet, variable reluctance and hybrid.
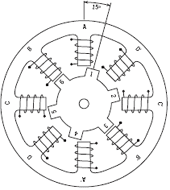 Variable-reluctance :
Variable-reluctance type stepper motors, that are the simplest type of steppers, consist of a soft iron multi-toothed rotor and a wound stator. When DC is applied to the stator windings, the poles become magnetized. Rotation occurs when the rotor teeth are attracted to the energized stator poles. Since the magnets of the variable reluctance step motors are smaller and lighter than those of permanent magnet step motors, they are faster. The smaller the area between the rotor and the stator gears of VR type stepper motors, the less the loss of the magnetic force.
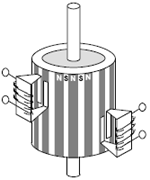 Permanent Magnet
As the name implies permanent magnet steppers have permanent magnets added to the motor structure. The rotor no longer has teeth as with the VR motor. Instead the rotor is magnetized with alternating north and south poles situated in a straight line parallel to the rotor shaft. These magnetized rotor poles provide an increased magnetic flux intensity and due to this the PM motor exhibits improved torque characteristics than the variable reluctance type steppers.
Hybrid
The hybrid stepper motors have the combination of the best properties of variable reluctance and permanent magnet steppers, so they are more expensive than the PM stepper motor. The hybrid type stepper motors provide better performance with respect to step resolution, torque and speed. The rotor of a hybrid stepper is multi-toothed like the variable reluctance steppers and it contains an axially magnetized concentric magnet around its shaft. The teeth on the rotor provide an even better path which helps guide the magnetic flux to preferred locations in the airgap.
The most commonly used types of stepper motors are the hybrid and permanent magnet. The designers preffer permanent magnets unless their project requires the hybrid steppers, since the cost of permanent magnet are less than of hybrids.
|
Bipolar and Unipolar Stepper Motors |
Stepper motors can be divided into two classes according to the type of winding as bipolar and unipolar steppers.
Unipolar stepper motors have one winding with the center tap per phase. Each section of windings is switched on for each direction of magnetic field. Because in this arrangement a magnetic pole can be reversed without switching the direction of current, the commutation circuit can be made very simple for each winding. Typically, given a phase, the center tap of each winding is made common: giving three leads per phase and six leads for a typical two phase motor. Often, these two phase commons are internally joined, so the motor has only five leads.
Bipolar stepper motors have a single winding per phase. To reverse a magnetic pole, the current in a winding needs to be reversed. Therefore, the control circuit must be more complicated. There are two leads per phase and none are common. |
Advantages and Disadvantages of Stepper Motors |
Advantages :
The rotation angle of the motor is proportional to the input pulse.
If the windings are energized, the motor has full torque at standstill.
They provide precise positioning and repeatability of movement, because good stepper motors have an accuracy of 3 – 5% of a step and this error is non cumulative from one step to the next.
They show excellent response to starting, stopping and reversing.
Since there are no contact brushes in the motor, the steppers are very reliable. The life of the motor is simply dependant on the life of the bearing.
The motors response to digital input pulses provides open-loop control, making the motor simpler and less costly to control.
It is possible to achieve very low speed synchronous rotation with a load that is directly coupled to the shaft.
A wide range of rotational speeds can be realized as the speed is proportional to the frequency of the input pulses.
Disadvantages :
Resonances can occur if not properly controlled.
Not easy to operate at extremely high speeds.
|
How to Use Stepper Motors? |
Since the windings of a stepper motor must be energized properly to achieve correct operation, we need to know not only the electric specifications but also the mechanical specifications when we use a stepper motor. Some important specifications are explained below.
Voltage and Current:
Mostly stepper motors have voltage ratings of 5,6,or 12 V. It is not recommended that you overdrive the windings of a stepper motor. Since unlike the conventional DC motors, you may burn the windings if you apply overvoltages of more than 30% of the rating. The rating of current depends on the application. Common types can draw currents in the range from 50 mA to 1A. The higher the current and voltage, the higher the torque.
It is important to consider that the current ratings are given per winding. So when designing a power supply for using a stepper motor, the power supply must be able to supply at least double the current per winding, or eight times the current per winding in a four-phase type.
Sequence:
When using stepper motors, you must determine the sequence of pulses taht produce correct operation.
Step Angle:
When a pulse in the sequence is applied to the motor, it advances one step, so the shaft moves a specified number of degrees. This step angle can vary depending on the type of the stepper motor.
Pulse Rate:
The pulse rate determines the speed of the motor. To determine the rotation per minute (rpm) of stepper motor, you should know the step angle and the number of pulses per second. For example if you are using a stepper motor with a step angle of 2 degree and apply 160 pulses per second, the motor will run at 1 rotation per second or 60 rpm. The stepper motors are not intended for high-speed applications. The top recommended speeds are in the range of 2 or 3 turns per seconds.
Torque:
The produced torque by a stepper motor is not very high. A typical stepper motor can provide only a few grams per centimeter when running. So, gearboxes must be added when high torque is needed. Since torque falls with speed, it is important to use these motors in low-speed applications.
|
References:
www.solarbotics.net/library/pdflib/pdf/motorbas.pdf Industrial Circuits Application Note Stepper Motor Basics
Mechatronic Sourcebook, Newton C. Braga, Thomson Delmar Learning |
|